
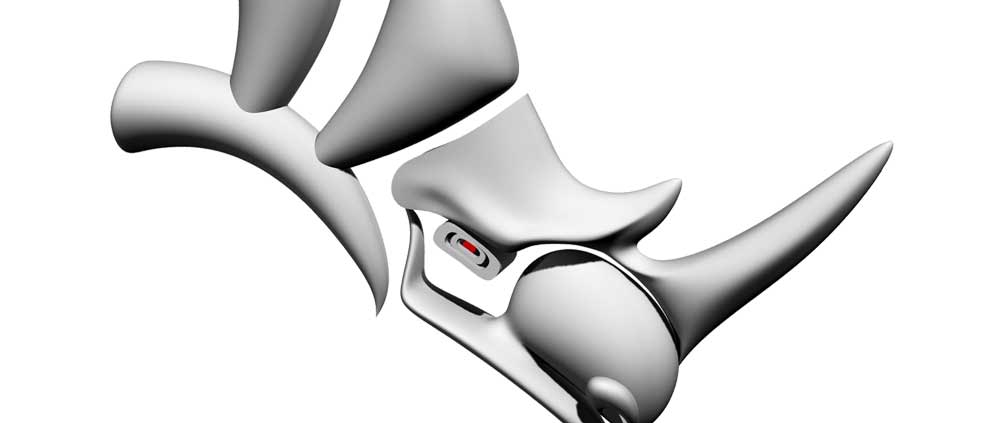
After a layer of the model, or ‘slice’, has been completed, a new layer of the powder is added on top of the powder bed.
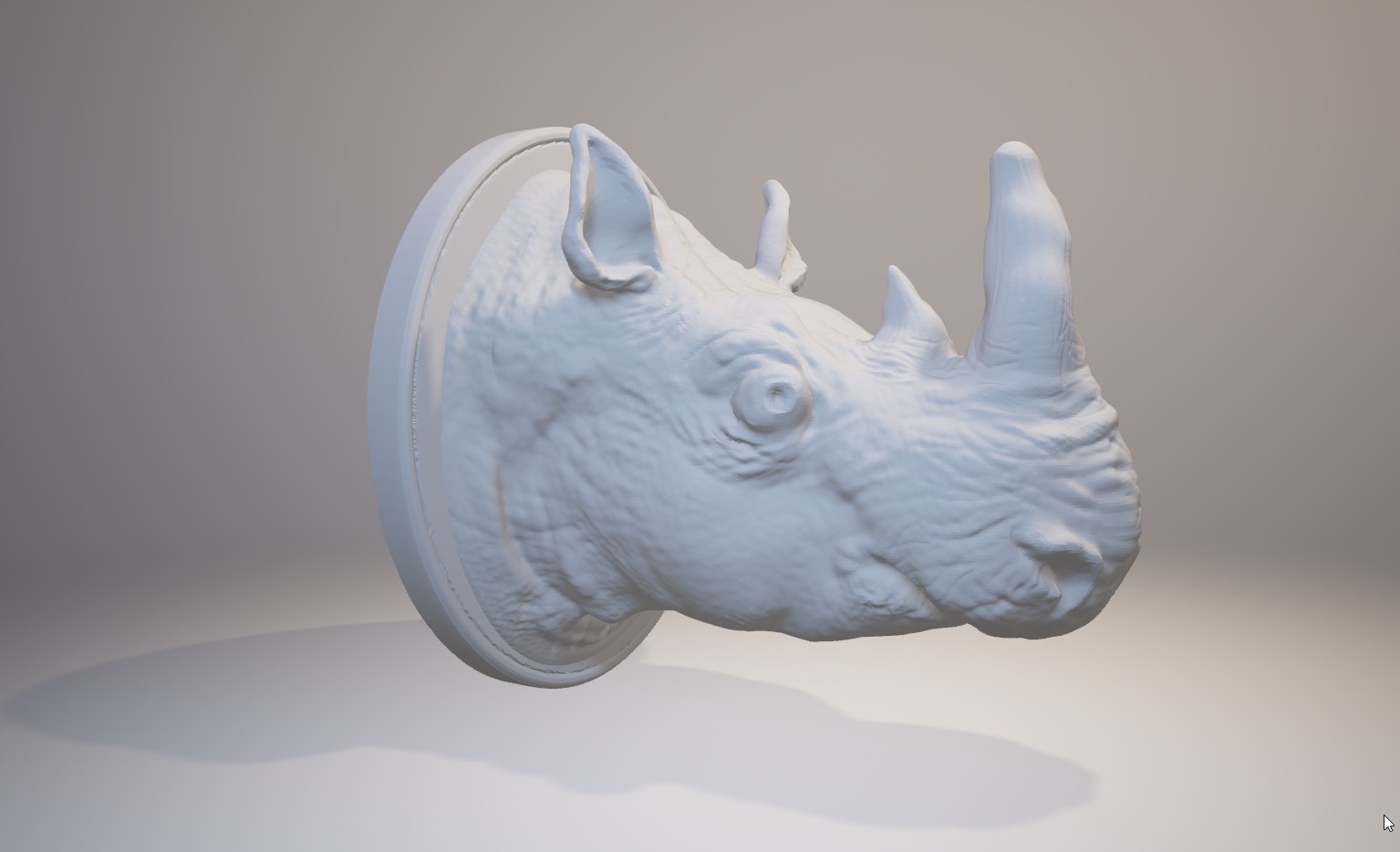
When the laser crosses the bed, it tips the temperature of the material just over the melting point, causing the powder to fuse together. The material is brought up close to its melting point by a radiant heat source, prior to the laser crossing over the bed of material. The model is built up out of layers of powder, which is placed in the printer. This technology uses a high powered laser to fuse powder made up of plastic, metal, ceramic or glass granulate to create the model. Another commonly known technology cures layers of liquid material to build a model, this is known as SLA (Stereolithography). SLS (Selective Laser Sintering) and FDM (Fusion Deposition Modelling) are the most common technologies using melting or softening materials in order to allow for the layers to be built up. Differences between technologies are mainly in the way layers are added together in order to create the model. Not every printer used the same technology to construct its prints, several ways of building a print exist and all of those technologies as of 2012 are additive.
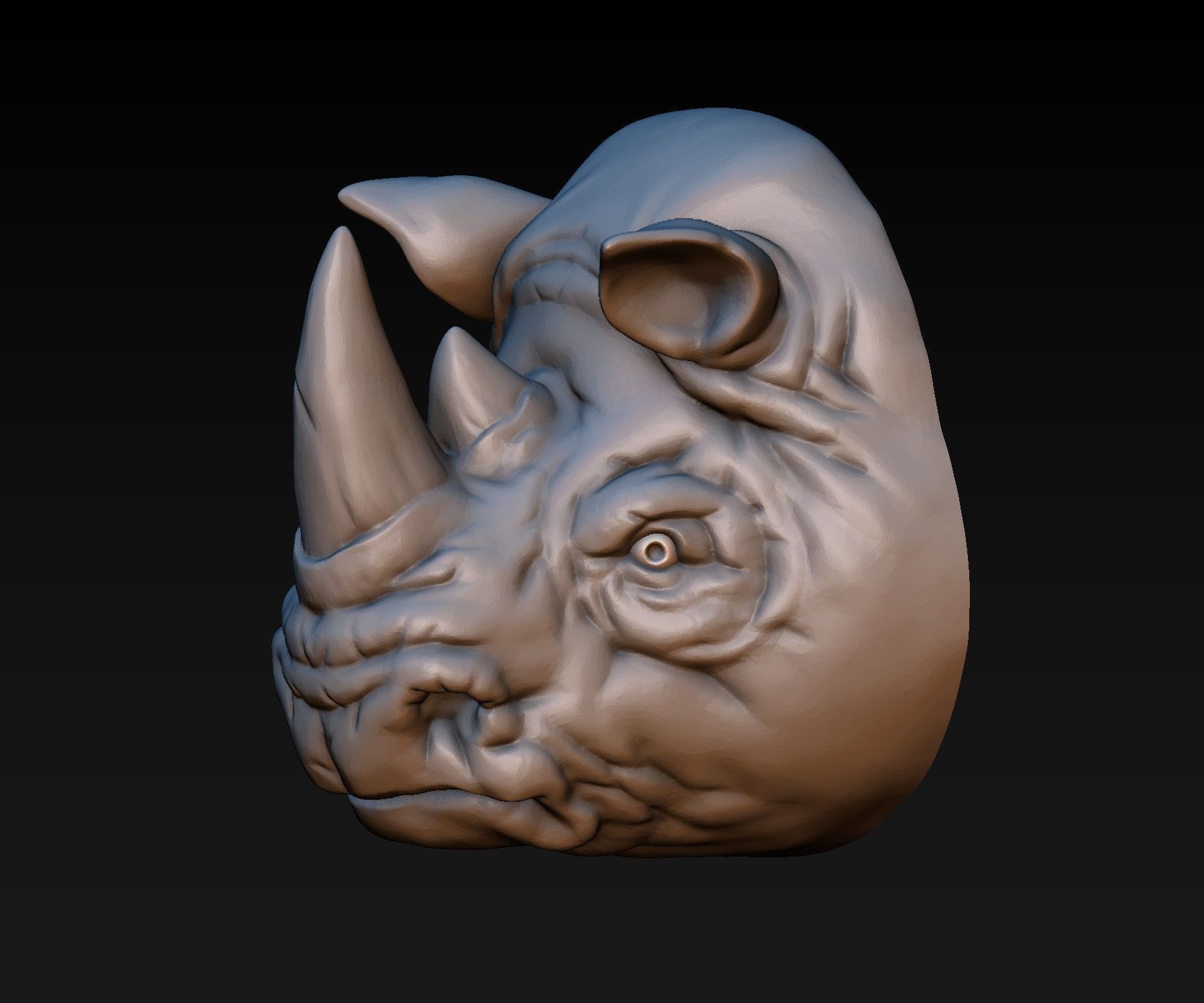
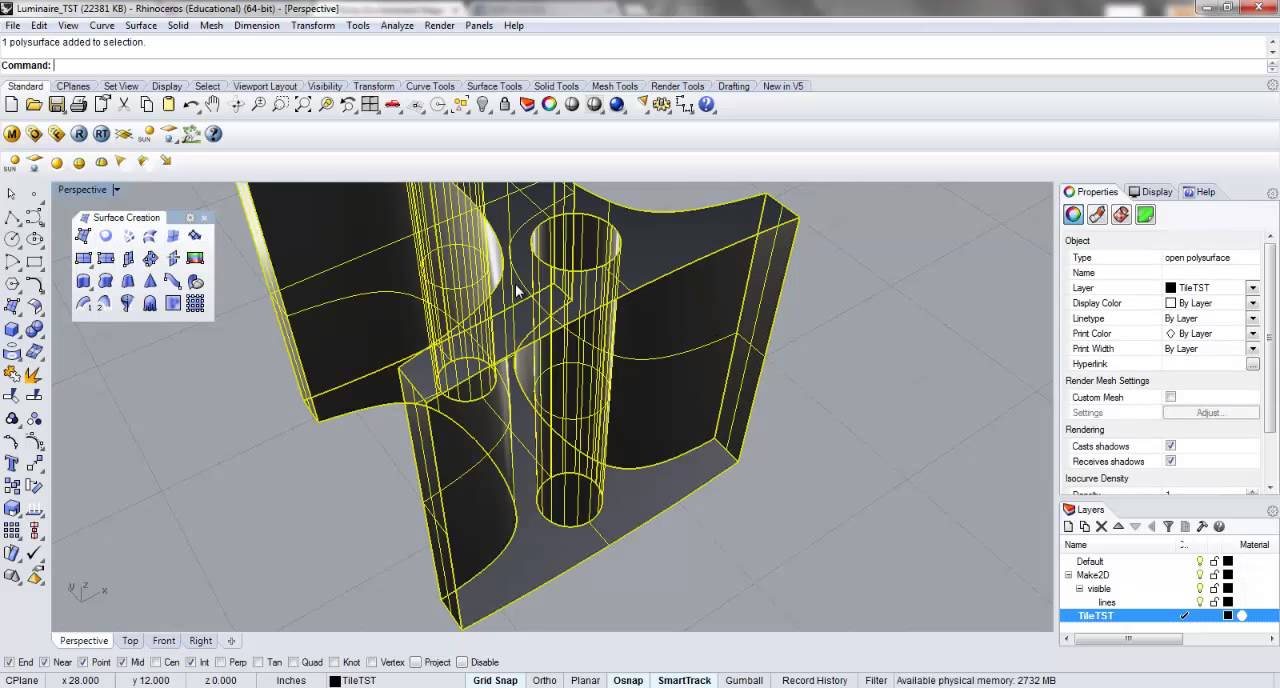
To prepare the design for printing, software creates these slices, which allow the printers to create the object layer by layer. These layers (slices), used to build the object, are thinly sliced horizontal cross-sections of the object. In additive manufacturing processes, subsequent layers of material are created to create a structure, resulting in a 3-dimensional object. These 3-dimensional designs can be turned into physical models using a series of techniques called additive manufacturing. Virtual designs are created using CAD (Computer Aided Design) software. A 3D print starts off as a virtual design of the object to be printed.
